Almost 15 years ago, the Museumsbahn e.V. came up with the idea of renewing the doors of the locomotive shed. All the gates were to be made in the historic riveted construction method. The design is based on that of the first “gate generation”, as they were installed in the locomotive shed until about 1945. In addition to their cultural-historical value, these gates offer the advantage that the upper half is glazed, allowing more light to enter the interior even when the gates are closed.
Finally, in the fall of 2008, the project to rebuild the locomotive shed doors was started in cooperation with the Ausbildungsverbund Metall (AVM) in Rüsselsheim. The AVM is a non-profit social institution active in the areas of training, qualification and employment. The new construction of the gates could be realized as an apprentice project within the framework of the training as a metal worker.
As a “prototype”, the gate on the rear side of the shed facing Steinstraße was first renewed, as it has different dimensions to the gates on the turntable side on the one hand, and on the other, initial experience for “series production” could be gained here.
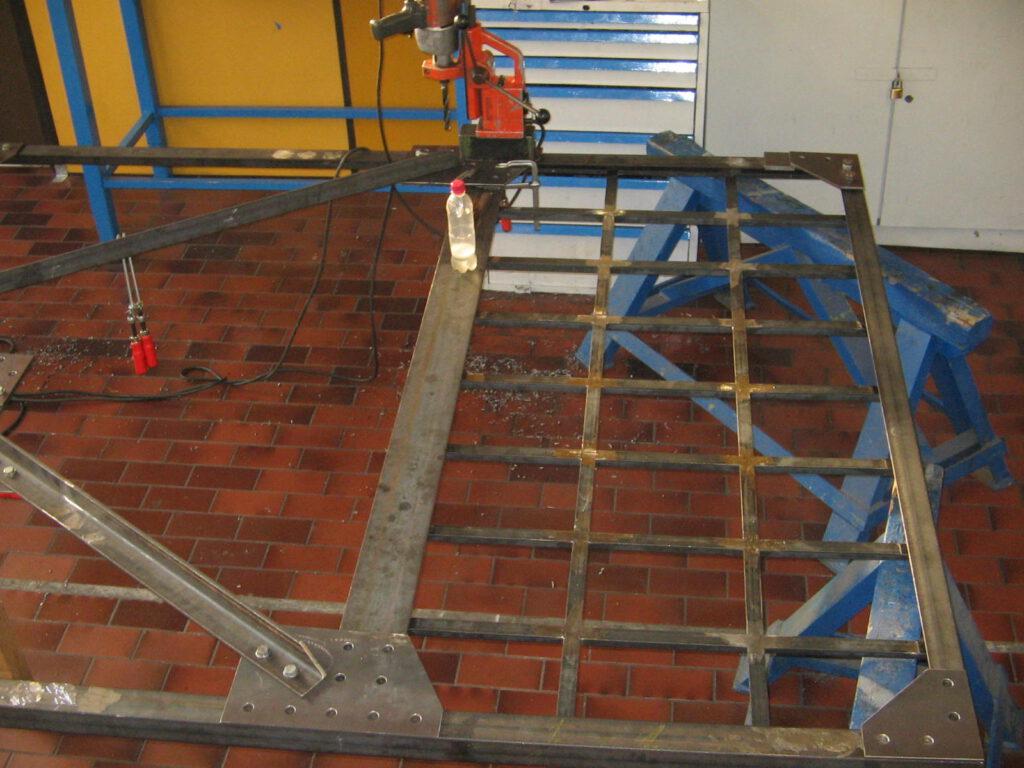
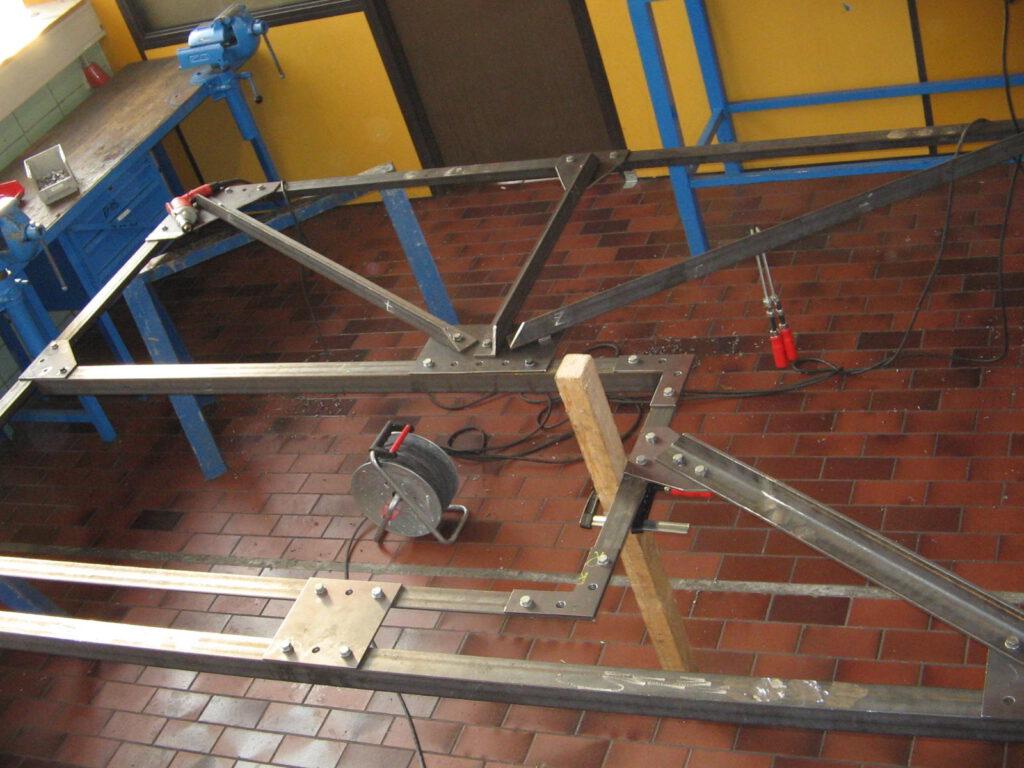
The rear shed gate was not only manufactured by the trainees, but was also installed on site at the railroad museum by the trainees themselves.
Approximately one year later, from the summer of 2009, series production of the front gate systems began.
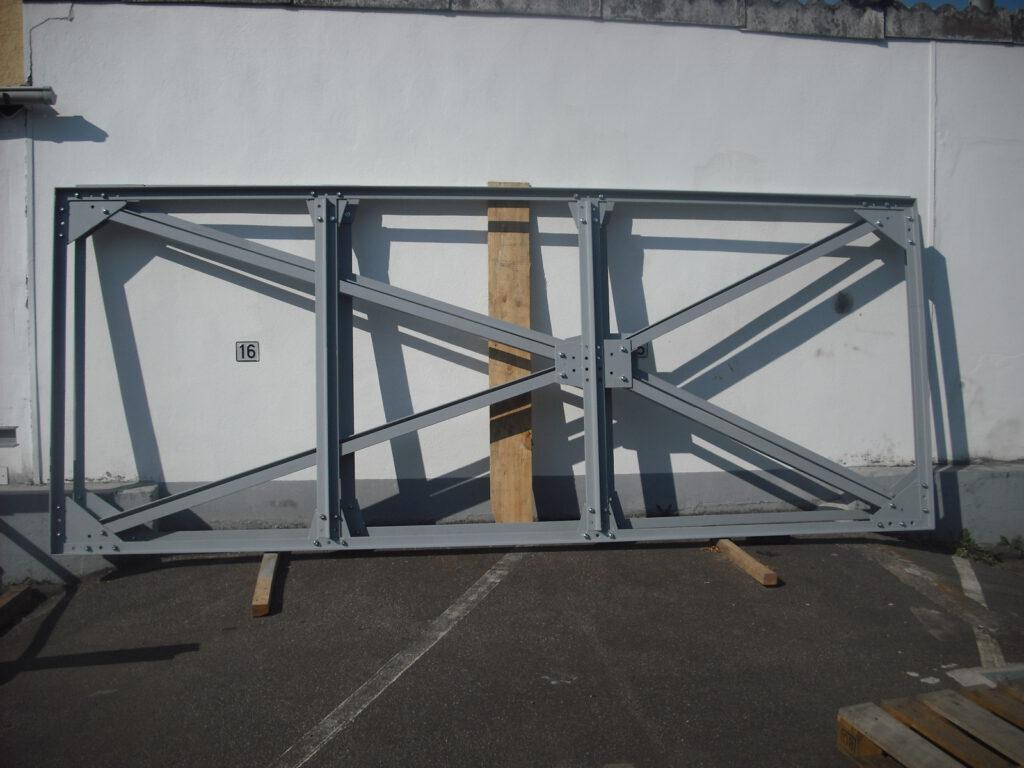
In October 2009, all 16 gate wings were ready for the riveting work that now followed. The museum’s 5-ton riveting machine was specially transported to Rüsselsheim for this purpose. As a workshop in the training, the topic of “hot riveting” was first prepared in theory and then implemented in practical work together with the workshop manager of the museum.
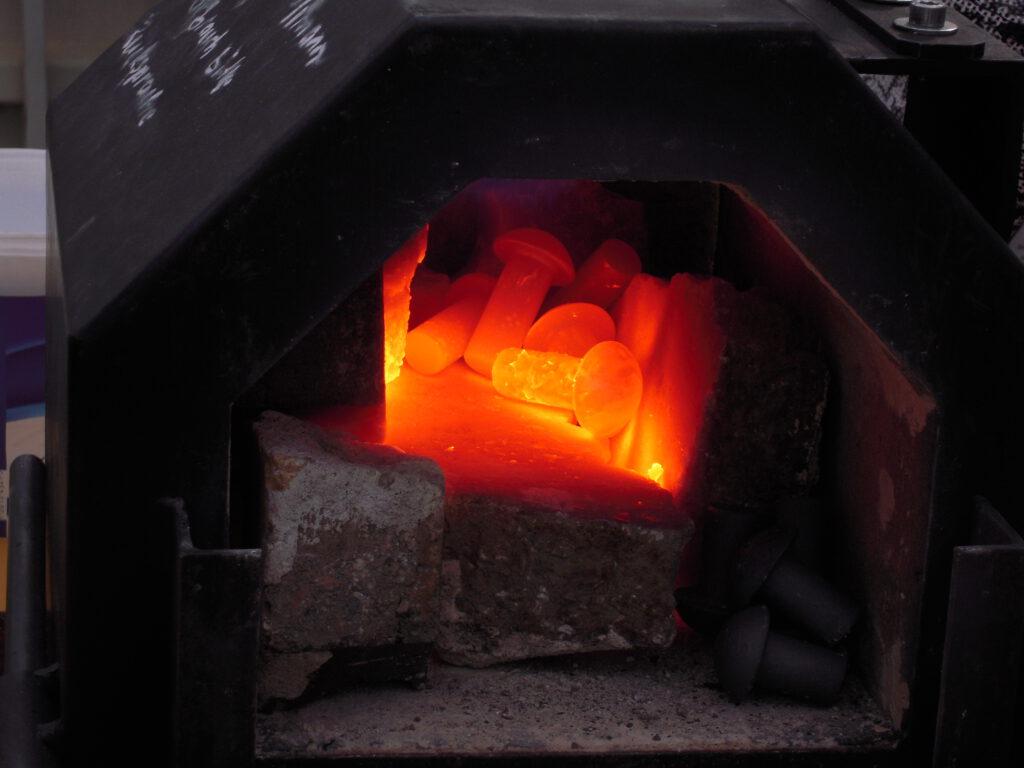
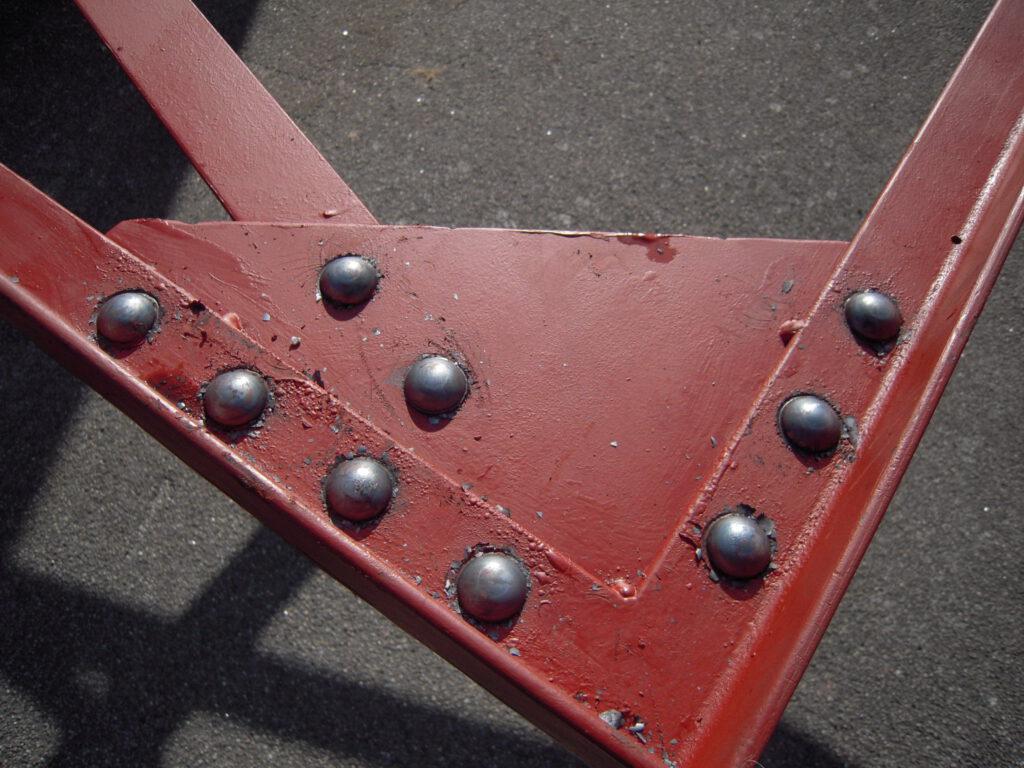
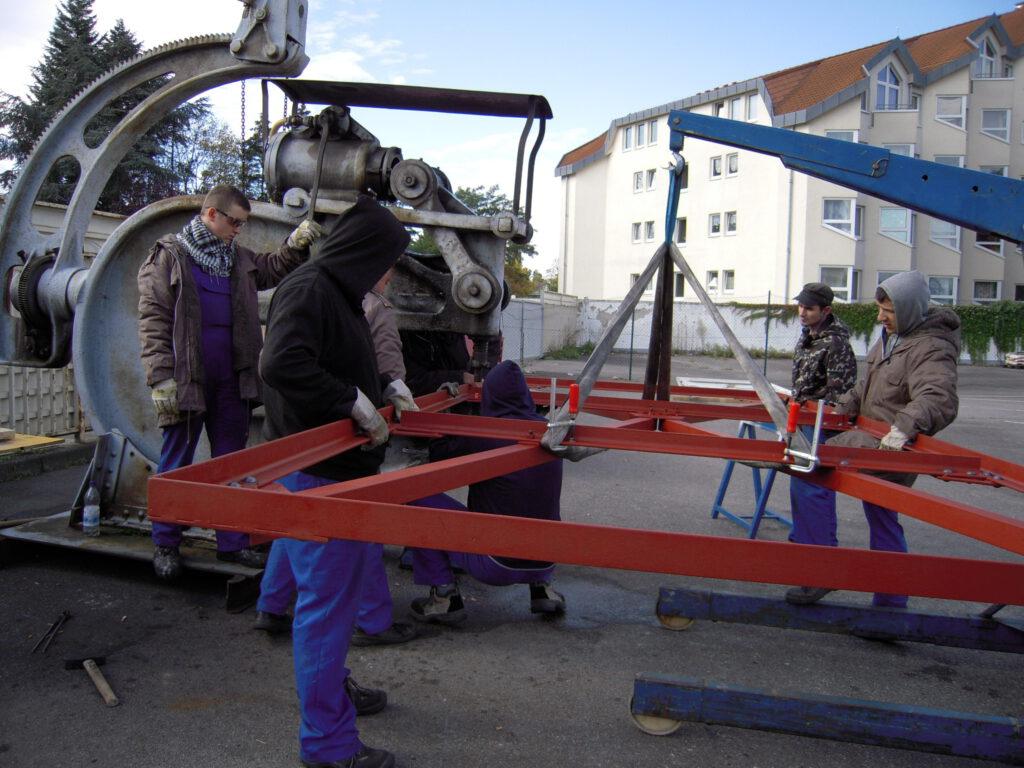
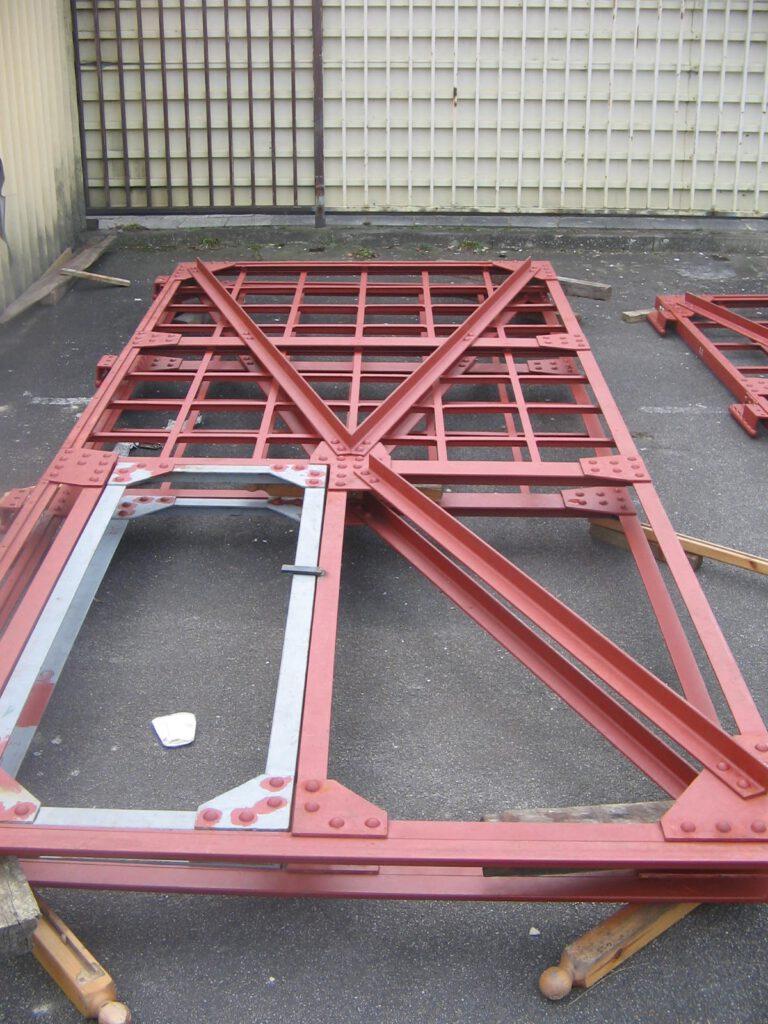
The completion of the gates should be done by the museum. Therefore, the work by the AVM ended at this point. At this point, our thanks go to the executing trainees under the direction of their trainer Mr. Bauer!
This was followed by years of painstaking work to paint all 16 sashes, conserve and install the wooden infill (approx. 64 m2 in double layer). The glazing of the window inserts proved to be a challenge. Here, the task was to glaze 768 (!) glass panes individually with window putty. One kilogram of putty was used per pane, so that in the end a total of approx. 770 kg of putty was used on all the doors.
A big thank you goes to the following companies who supported us with material:
- Company EGO GmbH for the donation of 400 kg of putty
- Karl Traser GmbH Fensterbau, Arheilgen, for the donation of 400 cut-to-size window panes
- Schreinerei Pfeiffer, Groß-Umstadt, for the donation of 400 cut-to-size windows
The assembly of the first front gate took place on June 22, 2019. A great help was the two-way excavator purchased shortly before. Again, it was important to gain sufficient experience so that an efficient assembly process resulted for the further gates. First, the old sheet metal gate had to be dismantled.
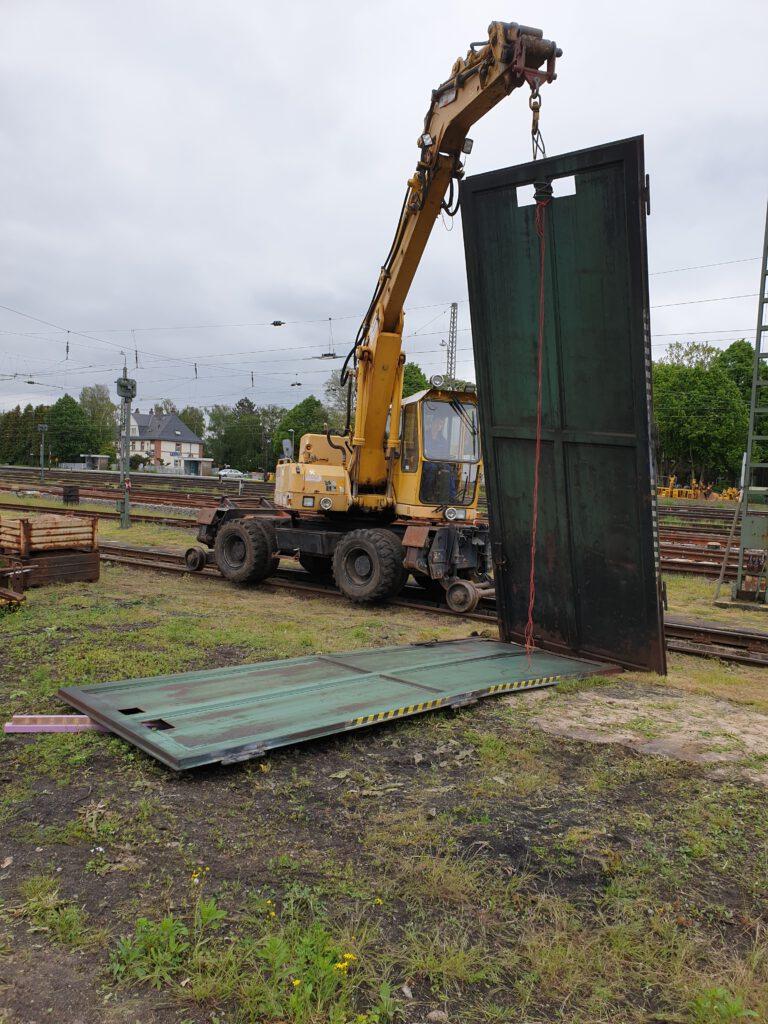
The next step was to place both new gate leaves against the front of the shed, secure them and mark the position of the hinges. Now the holes for the screw fastenings could be drilled. It took a whole day to get to this point.
Another day of work had to be invested to install the four window inserts and to do some small things for smooth operation of the wings:
- Mounting brackets with the gate open
- Glazing of the four mounting openings of the window frames
modification of the lower hinges due to the advancement of the roof beams of the shed - Adjustment of the closing latches
Because of limited manpower due to the priority given to maintenance and restoration of the company vehicles, further works were planned in such a way that two gates could be completed per year.
The last gate was installed before Christmas in December 2022. After completion of all finishing work (final painting and adjustment of the transoms), the project was finally brought to a close in March 2023.
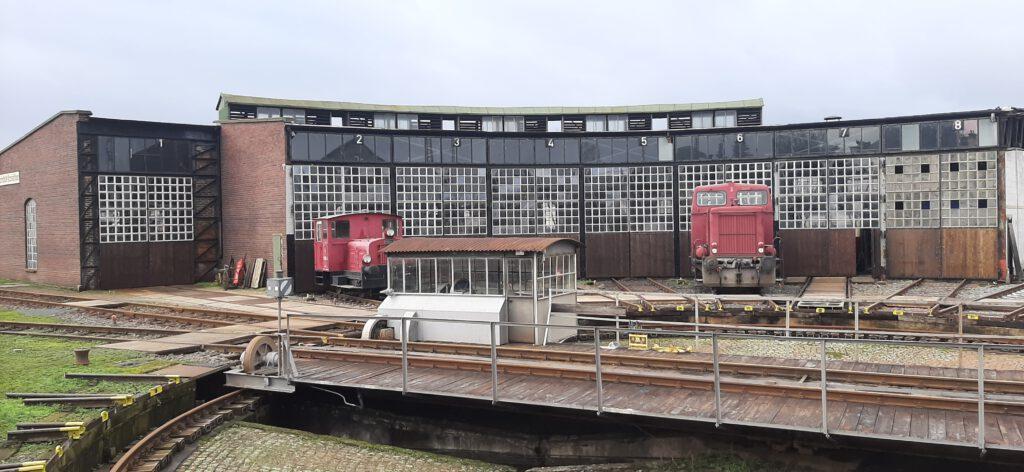
An additional task, which had not yet been taken into account in the project planning of the shed doors, arose in 2009 after the window front above the shed doors had been inspected. After a window pane there had come loose without permission and approached the ground in free fall (fortunately without personal injury), there was an urgent need for action here. With the Internationale Bund (IB), another social institution in Darmstadt could be won over for the replacement of the window strip. The IB also offers disadvantaged young people an opportunity to train as metalworkers. In addition to the production, the trainees also took over the assembly.
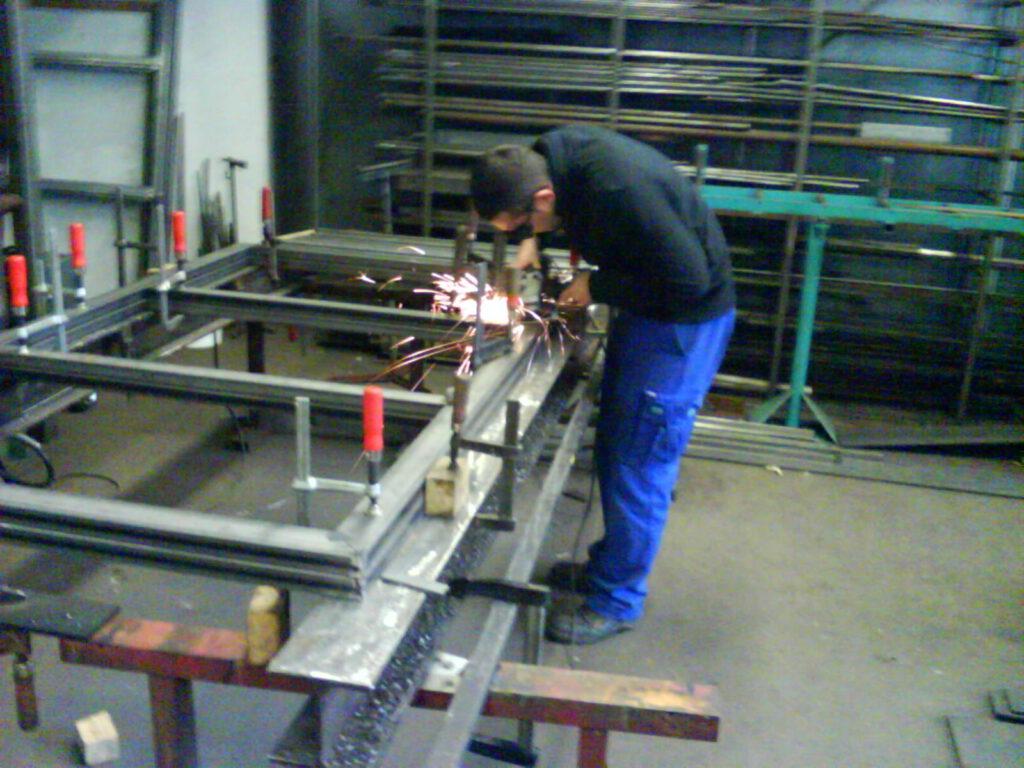
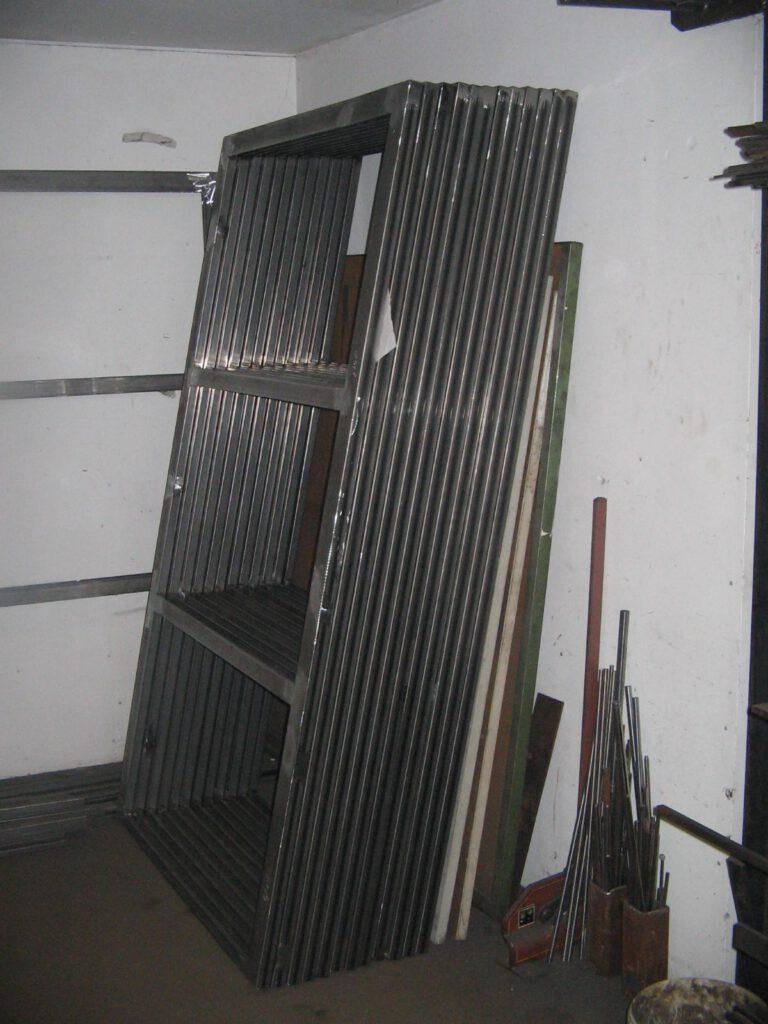
For the assembly of the frames, a scaffold was mounted on a flat car that could be moved from track to track. This meant that materials and tools were always at hand and laborious assembly and disassembly could be avoided.
Here, too, our thanks go to the trainees of the IB under the supervision of Mr. Dilling.
The glass panes were provided by the company Glas Meyer, Ginsheim. Many thanks for this.
Assembly of the window band by the trainees in the museum.